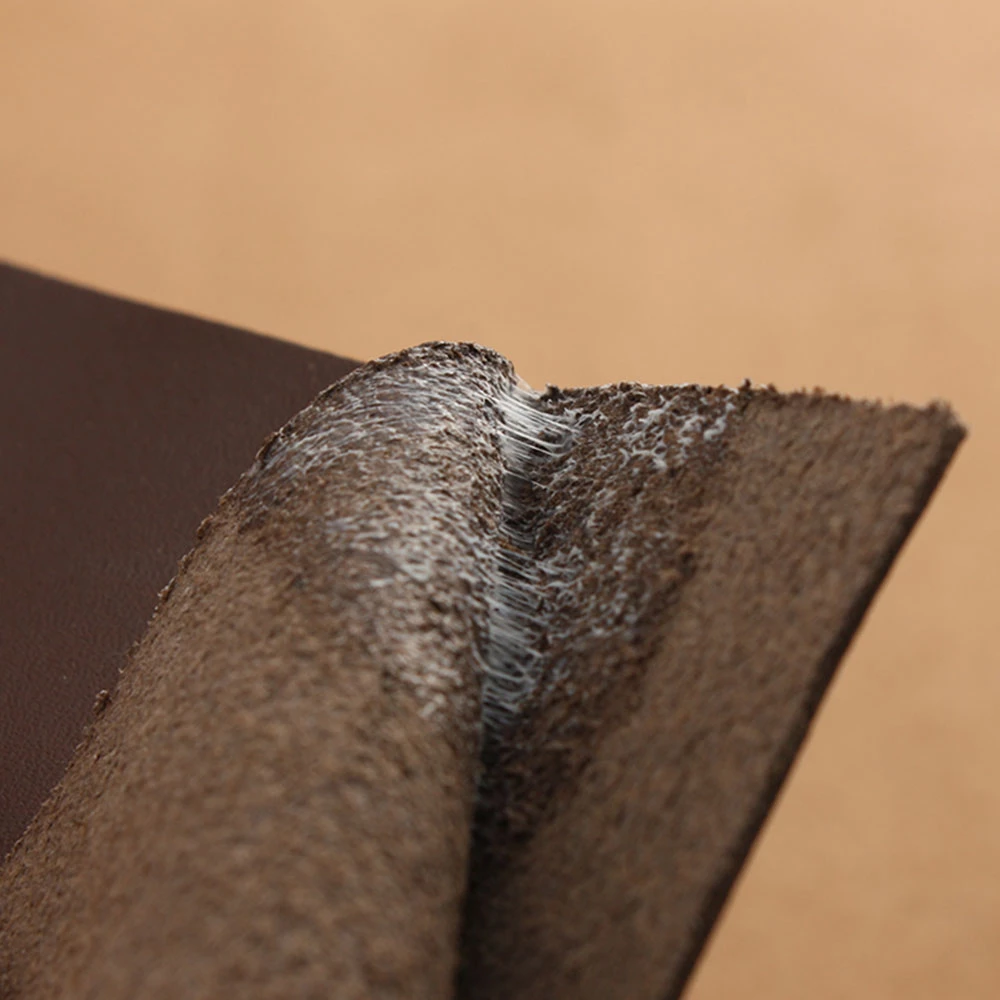
WBA Ecostick vs Other adhesives
Comparative Study: Intercom Water-Based Adhesives vs. Solvent-Based & Natural Rubber Adhesives
This study evaluates the performance, cost, and efficiency of Intercom water-based adhesives (Ecostick 9015st) compared to solvent-based adhesives and natural rubber adhesives in the footwear industry.
1) Methodology
A parallel test was conducted using 1,000 pairs of shoe uppers, with two different glue application methods:
1️⃣ Solvent-Based & Natural Rubber Adhesives:
- Applied manually using a brush and bottle.
- Yellow solvent-based NP glue & solvent-based rubber glue were used.
2️⃣ Intercom Water-Based Adhesives (Ecostick 9015st):
- Applied using an Intercom spray system.
- Ecostick 9015st water-based adhesive was used.
2) Quantitative Analysis: Cost & Efficiency
Cost Factors | Labor Cost/hr (USD) | Solvent NP Glue Cost/kg (USD) | Solvent Rubber Glue Cost/kg (USD) | Ecostick 9015st Cost/kg (USD) |
---|---|---|---|---|
Unit Cost | 2 USD | 2.5 USD | 1.5 USD | 8 USD |
Workers Required | 1 | 2 | 1 | 1 |
Hours Worked | 2 | 2 | 2 | 1 |
Glue Consumption (kg) | 2 | 2 | 2 | 1 |
Total Labor Cost/hr | 4 USD | 8 USD | 2 USD | 2 USD |
Total Glue Cost | 5 USD | 3 USD | 8 USD | 8 USD |
Total Glue + Labor Cost | 9 USD | 11 USD | 10 USD |
💡 Key Findings:
✅ Ecostick 9015st reduces glue consumption by 50%, requiring only 1 kg instead of 2 kg.
✅ Spray application saves labor costs, requiring only 1 worker for a shorter duration.
✅ Total cost per application cycle is lower for water-based adhesives compared to solvent-based alternatives.
3) Qualitative Findings
1️⃣ Product Quality
✔ Ecostick 9015st is resistant to aging & temperature changes.
✔ No yellowing or odor, maintaining the natural texture of shoe uppers even after one month of storage.
✔ No migration issues, preventing stains or defects on materials.
2️⃣ Work Efficiency & Workflow Optimization
🚀 Spray application is more efficient, reducing manpower requirements by up to 75% (1 worker vs. 4 for brush application).
🚀 No bottle refilling required, cutting down on interruptions.
🚀 Reduces the need for cleaning operations, preventing glue stains on the grain side of the leather.
🚀 Stacking & moving materials is easier – uppers do not stick together, reducing storage space and handling time.
3️⃣ Reduction in Defects & Waste
✔ Prevents staining & migration issues, saving defective pairs that would otherwise be discarded.
✔ Better QC output, increasing the percentage of accepted products in the final inspection.
4) Hardware Costs & Return on Investment
Expense | Intercom Spray System | Manual Application (Brush & Bottles) |
---|---|---|
Hardware Cost | 3,000 USD (depreciated over 10 years) | – |
Annual Maintenance Cost | 400 USD | – |
Brushes & Pipe-Bottles (Annual Cost) | – | 150 USD |
Total Annual Cost | 340 USD/year | 150 USD/year |
💰 ROI Justification:
- The Intercom spray system requires an annual investment of just 340 USD, which is easily recovered through savings on labor, material usage, and efficiency.
- Reduction in defect rates and quality improvements add an extra saving of 4,300 USD per month.
5) Total Cost Savings & Profitability
Factor | Estimated Monthly Savings (USD) |
---|---|
Labor, Material, & Time Savings | 10,000 USD (10 USD per 1,000 pairs, with 1,000,000 pairs/month) |
Reduction in Defects & Quality Improvements | 4,300 USD |
Total Savings per Month | 14,300 USD |
🔹 By switching to Intercom water-based adhesives, a company producing 1,000,000 pairs per month can save up to 14,300 USD per month!
6) Conclusion: Why Intercom Water-Based Adhesives Are the Best Choice
✅ 50% reduction in glue usage, cutting costs significantly.
✅ 75% lower manpower requirements, reducing labor costs.
✅ Higher product quality, preventing yellowing, migration, and defects.
✅ Improved efficiency & workflow, minimizing downtime and manual operations.
✅ Lower defect rates, reducing material waste & QC issues.
✅ Safer & environmentally friendly, eliminating VOC emissions & toxic solvents.
🎯 Intercom Ecostick 9015st + Spray System offers the best cost-efficiency, quality improvement, and productivity boost in footwear manufacturing. 🚀